How do you recycle composite from wind turbines?
When composite from wind turbines is to be disposed of then it either ends up in landfills, or it is incinerated. However, researchers are working on a sustainable way of recycling the composite material, says Mogens Hinge, expert in plastics from Aarhus University, in this blog post.
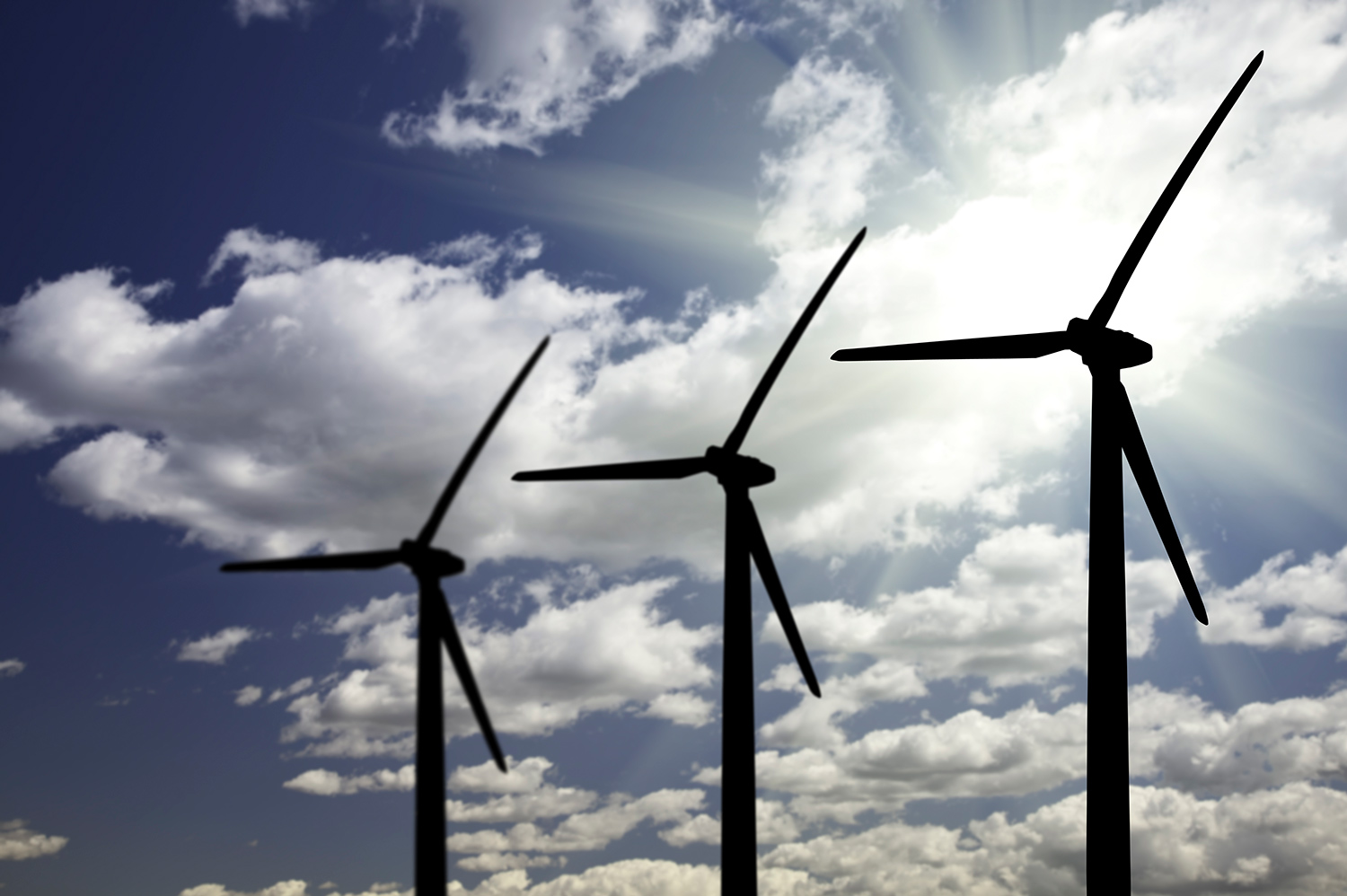
When a wind turbine is worn out, too small, and/or it is uneconomical to repair it any longer, it has to be decommissioned.
Much of the wind turbine is recycled, for example cables, gearbox, generator, tower, and so on. However it is difficult to recycle the composite parts, for example the wings and the nacelle.
The composite parts typically consist of fibreglass and a cured epoxy matrix. The strength of the composite comes from the glass fibres, and therefore you want to have as much glass in the composite as possible. The normal measurement of the amount of glass in composites is the fibre volume fraction (standard: 55% - 60% v/v). This measurement gives an impression of an close to 50:50 mixture between glass and matrix.
However, if you take one tonne of composite then there are between 750 and 800 kg of glass, while the rest is the epoxy matrix. Therefore, it is better to think of these composites as a lot of glass glued together with a little epoxy, or perhaps even as an epoxy-contaminated glass.
The matrix is important for keeping the glass in shape and as a 'carrier' of forces to the glass fibres. These are very strong forces, so the matrix is chemically (i.e. covalently) bonded to the glass fibre, and at the same time the matrix is cross-linked 'to itself' with chemical bonds.
This makes for a fantastic material when in use – but it is a nightmare to recycle.
Recycling today is down-cycling
Today, many are working hard to separate the composites again so that they can be recycled. Although the perfect solution has yet to be found. This leaves two general methods to dispose of composites: landfill or incineration.
A small proportion of the composites does find new life by cutting it up and using it in other industries (for example as a partition wall between livestock in pig stables).
Incineration is the most unattractive solution, as only the matrix that has a good energy release when burned. This means that only little energy is gained and there is a glass slag left behind. All that’s left is landfill, and waste can be buried locally, so there is no energy loss due to transportation to an incineration facility.
Now, anyone can see that this is not a good or sustainable option. In the ideal world, there might be a benefit in separating the fibre and the matrix so they can both be recycled in other products. However, the chemical bonds makes it very difficult to do.
A large part of the research has looked at thermally breaking down the epoxy matrix and then recycling the fibres and using the out gassed molecules to produce other chemicals. This process requires heating the composite to around 550°C to ensure complete break down the epoxy matrix. The glass also has to be heated to these temperatures which also requires energy. Additionally the glass fibre coating which ensures good adhesion to the matrix is also removed, and this, in turn, makes the glass fibres crisp/brittle.
The fibres remaining after pyrolysis can therefore often only be used in less demanding products such as fillers or chopped fibres in plastic products. Hence the search for methods to separate fibres and matrix continues.
Additives can solve part of the problem
In 2016, the DreamWind project was set up with support from Innovation Fund Denmark. The approach in the project was to design a matrix that could be separated 'on demand'. The project had four different approaches to achieving this, although only the additive approach will be described here.
During the project, many (80+) different chemical compounds were evaluated, and a dozen or so of them were selected for further investigation. Over six months it became clear that the principle of adding a 'guest molecule'/additive to the epoxy matrix, and thereby introducing a separation possibility, worked.
However, some of the additives required exotic (usually toxic) solvents to separate the matrix. One additive (cystine – the cysteine-depleting agent in amino acid) stood out from the others as a molecule from the green cycle that further introduced separation of the matrix by immersing in acetic acid.
Clearly we were very happy when we found this. Now we had to examine whether the additive changed the epoxy matrix to such an extent that it became unsuitable for composites. Therefore, the matrix was thoroughly examined for viscosity increase in the uncured matrix, curing times, post curing strength properties, dynamic, thermal properties and much more.
There were minor changes in a few parameters, but not in the critical parameters. Then focus shifted to the composite, its properties and the possibility of recycling the composites. This also worked, but it became clear that when the composite was reinfused after separation, it was not possible to get the entire matrix out past the fibres.
The reason for this was that the fibres are so tightly packed that, even though the matrix is divided into smaller pieces, it is trapped like a ‘bird in a cage’. This means that the fibre volume fraction became smaller and smaller for each recycling, and therefore the strength of the composite fell correspondingly. Therefore, even though we can recycle the composites then again only in less demanding products.
It is clear that the additives solution will not work for the current problem, but it could solve the problem of recycling composites in the future.
The post above has previously been posted on Ingeniøren.